Quality of a plastic tank depends on the materials and equipment used to make it. It also depends on each of the tanks components being properly manufactured. That is why, below you will find a manufacturing guide, and a list of factors involved.
Guide to make plastic tanks:
The manufacturing process of a plastic tank is very similar to carpentry work who use metals or wood-respectively- as construction materials, that is, it must first be calculated, then it is cut to finally proceed to the assembly of the tank, which in wood will be made with guide/nails and on metals and plastics by means of a welding process.
We are going to focus on this last part of the process-welding- and its different techniques to build a plastic tank for the chemical industry.
- Body:
When we speak of a cylindrical tank this is done by means of a first plate that when cold rolled and welded both edges, we archive the formation of this, if the diameter of the cylinder is large, several plates must be welded in a linear plane (on the lateral faces) to join them after rolling and create the circumference of the diameter required for the formation of the cylinder. The ideal process to join these pieces is through a butt fusion machine, which heats the lateral face of both plates to the fusion point, and then - when applying the appropriate pressure - the fusion between the two is archived throughout the entire length and thickness of both plates.
In the case of a rectangular tank, the formation of angles at 90° is necessary, which can be done by means of heat fusion at 90° (by means of the heat-fusion machine) or by means of bending the plate at 90° (by means of a bender), in such a way that the four corners of the rectangle are manufactured that once created, the additional plates must be welded depending on the length of the required rectangle either by means of thermofusion or by applying welding by means of equipment extrusion, until completing the length required for the formation of the tank.
- Roof and floor:
There are many forms of roofs and floors for tanks depending on the requirement of the tank in question. Ceilings can be made flat, with a waterfall, with a manhole or even without a cover and in the case of floors, these can be made flat, conical, sloping,etc. To ensure good weldability, all roofs or floors must be welded through plastic extruders, which generates a fairy wide weld bead that allows both the bead and the plate to be in contract over a greater range of surface and with the precise quantity in relation to the thickness of the plate to be welded. The versatility of plastic extruders and the wide variety of accessories for them helo us to apply welding even in complex places such as the corners inside the tank, also relying on different accessories that are available for this purpose.
- Connections and reinforcements:
When it comes to circular tanks, there are many ways to add reinforcement bands, especially in the joints between several cylinders when it is a high-rise tank, it is also necessary to add reinforcements on the roofs when the diameter of the same is large and overall if it carried a load on it, in the case of rectangular tanks, it is recommended to add steel reinforcements and these be covered by plastic linings to avoid corrosion since these will provide the tanks with a highly reinforced mechanical structure on the outside, without losing the advantages - for the part, internal - which offers a plastic tank will be in contact with the chemical.
Besides adding reinforcements in the rectangular or cylindrical tanks, these will always have connections (inlet or outlet), man inlet, internal partitions, breakwaters, etc. For wich it is also recommended that all the connections and accessories in the tank be welded through plastic extruders, both for their performance and for the safety that these equipment give us in the application of welding, when there are places that are difficult to access, there is the possibility of doing it by means of manual heat guns, knowing that the performance is much lower but compensating for this by the possibility of reaching those places.
- Double containment and non-slip floor:
There are processes that require placing external tanks as a double containment to prevent the chemical solution from being lost when a spill occurs in the main tank. This containment tank can also be designed by tank calculation software. One of the ways to manufacture them at an affordable cost is through panel-type plates, since they have a good mechanical structure, good weldability and the intrinsic advantages of resistance to chemical attack of plastic materials.
Sometimes it is necessary to place non-slip plates that function as floors in the vicinity of chemical tanks or in areas where there will be the presence of corrosive products, this in order to protect the floors of the plant, as well as help prevent-in case of a chemical spill-some type of accident involving personal that requires maintenance of the area.
- Leak tests:
Once the tanks have been manufactured, it's necessary to carry out a toughness testing process to ensure that it does not leak. The traditional procedure is to fill the tank with water to validate its tightness, however before filling it. It is recommended to do a test through a spark taster, which is a gun-shaped equipment that shoots a controlled electric discharge and making this discharge pass in the joints where the welding was applied, going through them with the gun while another person stops a piece of steel on the other side; in the event that the tester detects the piece of steel, it will generate an electric spark determining the existence of a leak at that point, which can be repaired prior to the filling taste to avoid wasting time and liquid in it. These equipments are essential in the case of not being able to do water filling taste in the container, having the certainty that if the testing procedure we will ensure and guarantee the tightness of the tank.
Do you require trainigng, or are you interested in plastic welding processes? Visit CESLA Centro de soldadura plástica and contact one of the advisors to obtain all the information.
Factors that influence the manufacture of plastic tanks:
When we have the requirement to manufacture a tank that will be in contact with chemical products, its is necessary to make some considerations in terms of being able to choose the most suitable material to be able to satisfy its needs. The most relevant factors are:
- Chemical resistance:
Depending on the chemical substance, its density and concentration we can have materials more or less resistant to the chemical agent.
- Work temperature:
The temperature of the medium is a factor that will determine the resistance of a material in said applications, as well as the usefull life of a tank. Having in the portfolio, plastics that resist temperatures above 100° C and up 152° C wich is the range where we find the bulk of the process.
- Siza and/or maximum capacity:
Thermoplastic materials have the ability to be molded to make practically any shape of tank, the most common being:
- Rectangular tank: Various design variants in width, length and depth, considering with or without metallic teinforcements, depending on the length and height of the tank.
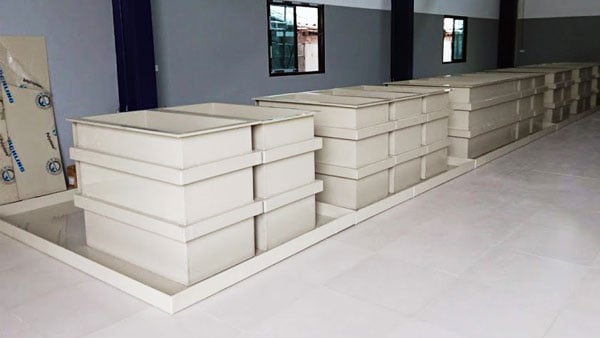
- Circular tank: allows the dimensioning of cylindrical tanks with a variety of designs on the bottom (conical or inclined), with a roof (flat or inclined) or even without a roof, etc.
- Exposure to UV rays (outdoors):
If the tank is located outside, factors such as exposure temperature and UV protection agents must be assessed.
- Tank building software:
There are several operating systems for the design of containers that make it possible to perform complex calculations of the thermoplastic material tanks for the manucafture of depressurized containers, in rectangular or cylindrical format, as well as to optimize the design of tanks according to the characteristics of the substance and the conditions, of the operation that said container is going to operate, wich can generate an engineering calculation memory based on the DVS 2205 regulations, wich becomes an optional guide for the manufacture of the container with the certification of the German standard.
Are you interested in learning more about how to design tanks? CESLA Centro de soldadura plástica can tell you how.
References:
Röchling. (2018). Fabricación de alto rendimiento para la construcción de depósitos e instalaciones químicas.
Leister. (2021, abril). Catálogo general - soldadura de plásticos.
CESLA. (2019). Manual básico de soldadura plástica. CESLA - Centro de soldadura plástica.